IM 75-B
A Potent
Inoculant for Gray and Ductile Cast Irons
In Gray Iron: Recent literature has shown once again that effects
obtained from the combined addition of two alloying elements are often
greater than the added effects of the individual elements. This same
type of synergistic effect has long been recognized with regard to the
role of Calcium and Barium in cast iron inoculation. The combination
of Calcium and Barium in IM 75-B provides a potent nucleating effect
with about 40% less IM 75-B needed to obtain equivalent chill depths
produced by the use of standard inoculating grade ferrosilicons. At similar
addition rates, IM 75-B produced dramatically lower chill depths than
standard inoculants, at all Carbon equivalent levels.
IM 75-B is particularly useful in higher strength, 3.6-3.8 Carbon equivalent
irons, in which inoculation would be expected to have the greatest effect
on improvement of mechanical properties. The combination of Calcium and
Barium minimizes undercooling, and promotes eutectic solidification with
Type A graphite and a pearlitic matrix. The comparatively high Silicon
content of this alloy further serves to increase eutectic cell count,
ensuring optimum properties from a given Iron analysis. Because the alloy
is based on 75% ferrosilicon, its reaction with liquid iron is exothermic,
ensuring excellent dissolution and consistency of results.
In Ductile Iron: Alloys containing over 70% silicon have long
been the favored inoculation material for ductile iron. In special carbideprone
work, many commercial foundries have reported increased nucleation and
elimination of chill because of the more potent effect of Calcium plus
Barium. During a two day trial in a commercial foundry comparing a Calcium
plus Barium alloy a regular Calcium bearing ferrosilicon and a high Aluminum
European inoculant, the Calcium plus Barium alloy produced nodule counts
18% higher than either of the other two alloys.
IM 75-B can be used in all grades of ductile iron.
IM 75-B is produced in state-of-the-art submerged arc furnaces in one
of the newest ferrosilicon plants in the world, completed in 1980. By
using charcoal and iron ore in place of metallurgical coke and steel
scrap as reducing agent and iron unit source, respectively, residual
levels of harmful tramp elements are controlled to extremely low levels.
The manufacturing operation is supported by an in depth quality program
devoted to problem prevention through the application of statistical
control techniques. This is a unique combination of modern facility and
quality attitude aiming to provide products that consistently conform
to specific customer requirements.
Specifications
Chemical
Analysis: |
|
3/8"x20M
/ 6Mx20M |
20Mx80M |
Silicon |
74-79% |
70-75% |
Calcium |
0.8-1.3% |
0.8-1.3% |
Barium |
0.8-1.3% |
0.8-1.3% |
Aluminum |
1.20%
max. |
1.20%
max. |
|
|
Effective
Date: 3/28/06 |
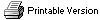 |
Please
Note:
Product specifications are subject to change
|